Let’s take independent suspension as an example to learn more about the structure and working principle of the suspension. The most typical independent suspensions are the McPherson suspension system, double wishbone suspension, and multi-link suspension. The suspension system includes the wheel hub assembly, suspension links, control arms and beams, springs, shock absorbers, lateral balance bars (anti-roll bars), suspension mounting elements and other components. First of all, the entire wheel hub assembly consists of the wheel hub, wheel hub bearing, and steering knuckle. The wheel hub is installed on the steering knuckle. The steering knuckle is also called the horn. It has a wheel hub bearing inside. After the three are connected, they are connected to the control arm through the steering knuckle. The wheel hub is connected to the brake disc and the wheel. The steering knuckle is connected to the tie rod in addition to the control arm. In addition, the brake caliper is also installed on the steering knuckle. When the steering wheel turns, it drives the steering knuckle to move, and then drives the tie rod to move. The tie rod drives the steering knuckle to move, so that the wheel rotates to realize the steering function. Next is the suspension link, control arm and beam. In order to enable the wheels to move within a controllable range, each link, control arm and beam are indispensable. These components can also transmit the horizontal and longitudinal forces from the road surface.
Let’s continue to look at the coil spring and shock absorber. The two of them are combined to form a shock absorber pillar, which supports the weight of the vehicle body. When there is an external force pressing down, it will compress and deform, and when the external force is released, it will return to its original state. Therefore, the role of the coil spring is to absorb the vertical force of the downward pressure during the compression stroke of the vehicle body to mitigate the impact. In addition to coil springs, there are torsion bar springs, leaf springs and air springs. The torsion bar spring is a metal rod that can be twisted. It is rare in modern cars, but it often appears in many tracked vehicles. It can achieve a torsion effect. The leaf spring should be very common. It is made of stacked multiple steel plates. It is often seen in many cars and trucks. Its characteristics are strong bearing capacity but very hard. The air spring is a compressed gas filled in a sealed container, and the compressible characteristics of the gas are used to achieve elasticity. The pneumatic suspension system with air springs has good ride comfort, but due to its complex design and high manufacturing cost, it is generally used in high-end cars. Let’s look at the shock absorber. The role of the shock absorber is to suppress the rebound of the vehicle body and play a damping role. When the coil spring is pressed down and the external force is released, the spring will rebound several times after returning to its original state. These rebound actions are the characteristics of the spring component itself. If shock absorbers are not used to prevent the coil spring from rebounding, the vehicle will continue to shake vertically up and down when passing through the shock absorber belt. Therefore, the role of the shock absorber is to suppress the rebound during the extension stroke of the suspension and allow the vehicle to quickly restore balance.
Let’s look at the lateral balance bar, also called the anti-roll bar. The function of the anti-roll bar is to prevent the vehicle from rolling when turning. It is a U-shaped metal rod. Its central part is fixed to the subframe by a rubber bushing, and its two ends are connected to the suspension through two connecting rods. When the wheels on both sides pass through uneven roads at the same time, the anti-roll bar will rotate up and down with the bushing as the axis. At this time, the amplitude of the left and right wheels is the same. If only one side of the wheel passes through a concave road, the anti-roll bar on the same side will be forced to twist and press down. Since the anti-roll bar has a certain toughness, it will drive the other side and there will be a tendency to press down synchronously. The same effect is also achieved when it bounces upward. In this way, when the left and right wheels pass through uneven roads, the two wheels will inhibit and rely on each other, which can play a role in suppressing vibration and stabilizing the vehicle body. Next are the components used for suspension installation, including rubber bushings, ball joints, upper support brackets, anti-roll bar bushings and sub-brackets. The rubber bushing is composed of two layers of metal bushings with rubber pads embedded inside. It is a common connecting element. The fixation of control arms, torsion beams, shock absorbers, etc. all rely on this component. In the middle of the ball joint is a ball stud, which is wrapped in a metal shell on the outside and filled with plastic on the inside. The ball stud can swing and rotate. The connection between the control arm and the steering knuckle is made of a ball joint. The ball joint can be an independent component or integrated with the control arm. The ball joint can also be seen in the anti-roll bar and steering system, such as the connection between the anti-roll bar and the control arm, and the connection between the outer tie rod and the steering knuckle. Next, let’s look at the installation of the shock absorber. The upper strut support is connected by a rubber pad. At the same time, since its bottom needs to rotate with the control arm, there is a strut bearing in the middle. Of course, in the double wishbone suspension, the shock absorber does not need to rotate with the control arm and only bears the longitudinal load, so the lateral stiffness is large and the operability is strong. The fixation of the lateral balance bar is relatively simple. It is first clamped with an open plastic bushing and then fixed by a metal bracket. The lateral balance bar can rotate freely in the bushing. Finally, let’s look at the subframe. The subframe is the installation base for other components. It is connected to the vehicle body, so it must be rigid enough. The subframe can be installed on both the front and rear axles of the vehicle. In addition to supporting the steering knuckle and suspension system, the front subframe also serves as the installation base for other mechanisms such as the engine, transmission, and steering system.
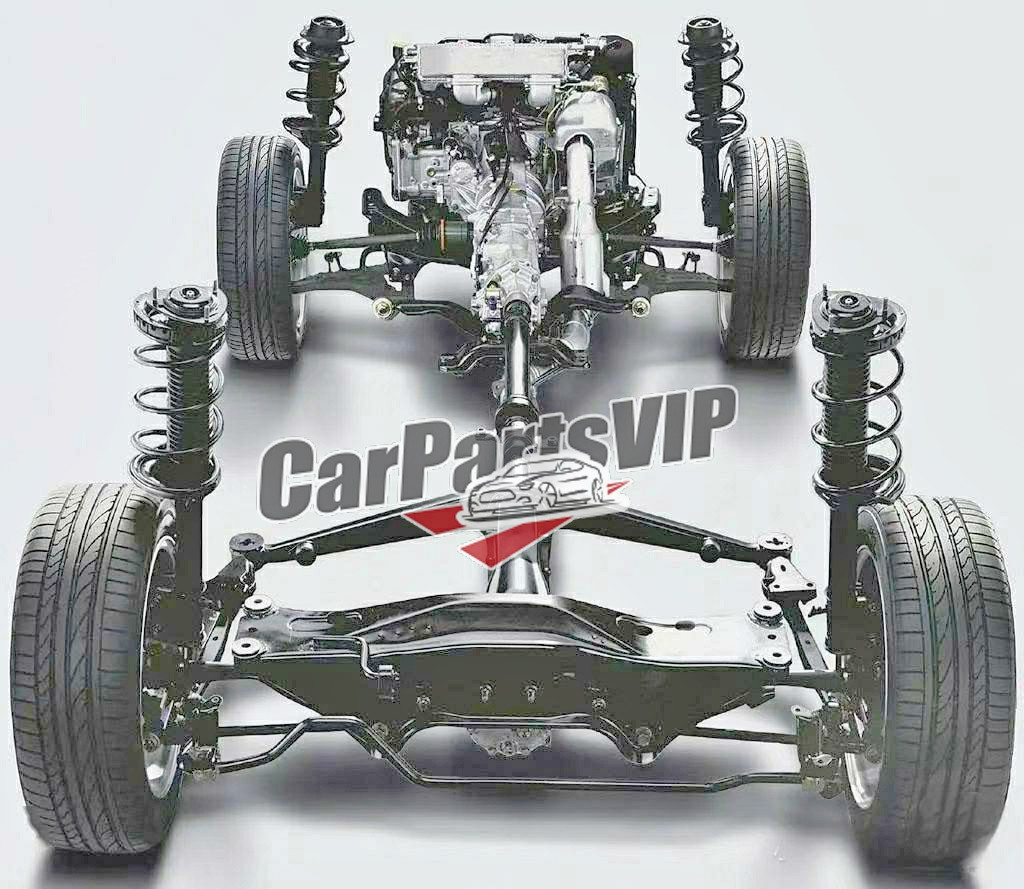